Circular Plastics: Designing Our Tupperware as Mother Nature Would (The Century of Biology: Part II.V)
Since the invention of plastics a century ago, they’ve become absolutely ubiquitous – you interact with them hundreds of times every day in every component of your life. Why? Well, they’re among the greatest products ever invented. They’re dirt cheap, perfectly uniform, lightweight, can be flexible and / or durable, waterproof, long-lasting, odorless and generally resistant to heat, cold, acid, fungi, and alcohols. As such, the industry has grown to be valued at over $650B. The flipside of plastic’s wonderful physical durability and long-lasting nature is it’s notoriously difficult to recycle. It’s generated 8.3 billion metric tons of waste, roughly the weight of 25,000 Empire State Buildings. Of that, 80% has ended up in landfills while just 9% has been recycled. Here’s a good summary of how difficult making the products we love fully reusable, especially durable goods:
So think about like a sneaker. It's made of all kinds of different material that's glued or stitched together in a way that would be very time consuming and require a lot of labor to deconstruct into something that's reasonable to melt down and use to create some other product. So this is part of why it is so difficult to increase that recycling rate. It's tough to get the stuff back, but even if you get it back, it's really difficult to sort it out and isolate all of these different kinds of polymers that we use together for many of the products that are that are super useful to us. And so much of the recycling that we do today is really what we call down cycling. We'll take a product we can shred it, melt it, reintroduce it into a new product, but that might still have dyes and additives and it's a mixture of all of these waste products that have all been kind of tailored differently for their original use cases. And so what you get out has the whole stuff in it that you didn't actually necessarily want. And so to achieve the same kinds of properties that you need, you very often blend that material with more virgin polymer. So you might only have like 10% recycled material in a product or 20%. Every time you recycle the material, you degrade the quality. So the length of the polymer chains is important. And just like the fibers in your clothes, longer is better, longer is stronger. But over time, through shredding, melting it down, reforming it, you end up with shorter and shorter polymer chains until you have something that is significantly degraded in terms of its mechanical qualities. So even if you didn't have the dyes and stuff in there, there's you can only recycle it for a limited number, let's say five cycles before it's just not usable anymore.
Making a product at plastics’ scale (roughly half a billion metric tons of product a year) that competes directly on performance and cost without using oil (an input already as ubiquitous and cheap as the outputted plastic) and that biodegrades only when we want it to is a Herculean scientific, technological, engineering and manufacturing effort.
That work began several decades ago. The biopolymer industry now produces roughly 2 million tons of 100% bio-based goods a year and has a market size of $9-12B.[1] It’s now become a focus of the US government, with the Biden administration aiming to displace more than 90% of fossil fuel–based plastics within 20 years.1 Moreover, many of the national science laboratories are working on the problem.[2]
The most commonly product to date, PLA, is made from sugars found in crops like corn and sugarcane. An issue with anything made from a biomass like corn stock designed specifically to biodegrade starts with the opposite performance traits as traditional plastics – think of paper straws or imagine your food container teaming with mold. Consider these theoretical qualms from plastics customers from this blog:
- Food packaging: So your polymer degrades by being food for fungi. Does that mean fungi will be growing in the food it’s packaged with?
- Consumer packaged good packaging: Will my child’s Barbie be moldy by the time she takes it out the box?
- Medical equipment: So, how long till it starts to degrade? Can we sterilize it?
- Personal care product packaging: Is this resistant to hyaluronic acid?
- Construction products: Our customers want our products to last a lifetime
- Electrical insulation: Will this degrade in the walls of a house? Is this a fire hazard?
- Aerospace interiors: Does your stuff burn? Can we load it with fire retardant?
Beyond performance issues, biopolymers made with primary agricultural biomass have a cost and environmental impact floor at the levels of industrial farming. For instance, switching packaging plastics to biopolymers would require 54% of current global corn production and 60% more freshwater withdrawal than Europe’s annual total.
With that in mind, more creative options like using waste or GHGs must materialize at scale. More than 1 billion tons of agricultural and food waste are produced every year, and plenty more biomass waste comes as bioproducts of lumber yards, paper mills[3], etc. Seaweed and algae have also been explored given their carbon-sinking nature. Additionally, CO2 captured from factories or directly from the air can be used converted into polymers with the right catalysts. Exhaust gases from ammonia factories and coal power plants contain ~97% and 15% CO2 (sold at <$70 per ton), respectively versus 0.04% in the atmosphere.
Indeed, as seen in the chart below, much of the work has gone into finding the right feedstock as well improving performance and cost characteristics of those products as seen in the graph below. See these studies1,2,3,4,5 for a breakdown of each kind of biopolymer.
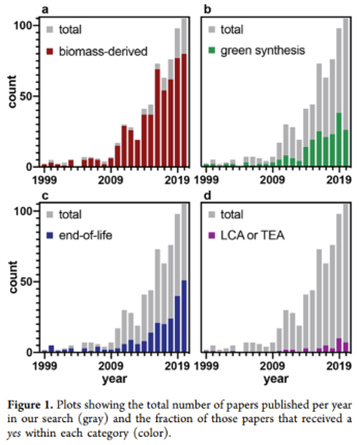
There have been several broad approaches to decreasing the amount of non-recyclable plastic being produced each year and / or properly recycling that which is already in existence:
- Engineering processes to use waste or GHGs as feedstocks
- Fully compostable or infinitely reusable (bio)polymers
- Additives for otherwise non-degradable polymers to make them programmatically degrade
- Degradation of existing plastics
Here are some of the top companies using biological methods to make more circular plastics:
- Engineering processes to use waste or GHGs as feedstocks
A company called Origin Materials uses acid hydrolysis to turn cellulose waste products like wood chips from lumber yards into a chemical that’s the building block for things like PET. On a weight basis, wood chips are 3x cheaper than oil, and because they’re the waste bioproduct of timber production, using them to make plastics adds no emissions to the environment. In fact, they claim their products are carbon negative. It’s building out two commercial scale plants and has inked over $9B in offtake agreements for its products with companies including Ford, Netsle, LVMH, Mitsubishi, and PepsiCo.
A startup spun out of the Wyss Institute is concentrated on making biodegradable polymers with the lowest carbon footprint instead of aiming to reuse the same polymers indefinitely without performance loss. They feed their microbes with carbon dioxide and hydrogen rather than the common practice of using sugars from plants like corn stover in the example above — the outputs of carbon-intensive agriculture. The carbon dioxide would come from direct capture at point sources like breweries, steel mills or ethanol production facilities. They engineered a microbe to convert the CO2 into sucrose which is in turn used as feedstock for E. coli. The graph below shows the product’s estimated sustainability improvements across a number of vectors, showing exciting promise.
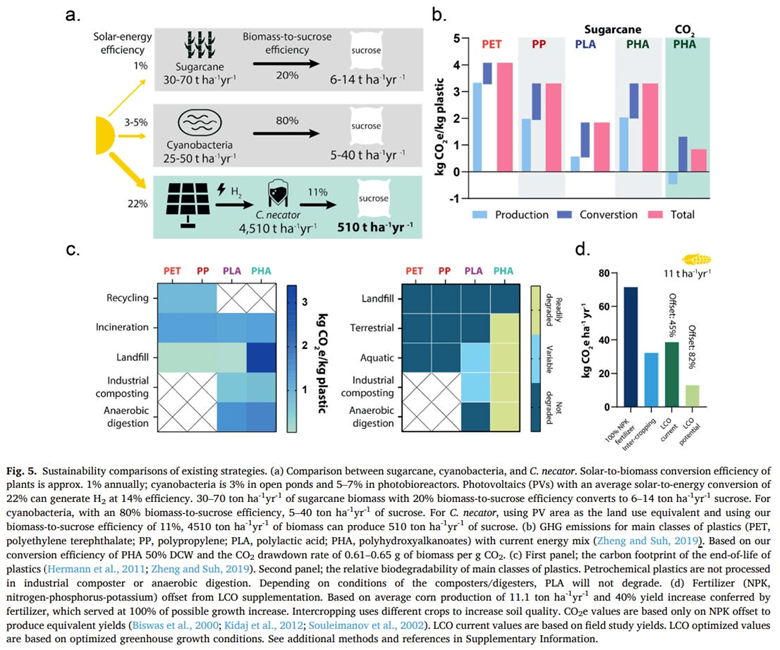
Here’s a summary of other research in the field:
Among the different approaches developed, utilizing CO2 as the raw material for the production of more valuable chemicals has attracted great research attention (Liu et al., 2015; Li et al., 2018). Among various CO2 valorizations, microbial fermentation for PHB production has gained great attention in recent years. C. necator, which is a gram-negative facultatively chemoautotrophic bacterium, is able to assimilate CO2 to produce PHB through the Calvin–Benson–Bassham (CBB) cycle (Bowien and Kusian, 2002). Unlike other organic carbon sources, which require heterotrophic growth, C. necator can utilize CO2 through H2 oxidation under autotrophic growth conditions (Li et al., 2020). Ishizaki and Tanaka (1991) attempted to utilize a gas mixture (H2:CO2:O2=75:10:15) as the carbon source and achieved 60 g/L biomass accumulation and 60% PHB content. Later, Mozumder et al. (2015) studied the effect of gas mixture composition and developed a corresponding model to find the optimal gas composition for PHB production, where a maximum biomass accumulation of 60 g/L and PHB content of 82% occurred at the gas composition of H2:CO2:O2=75:10:15. Moreover, to ensure the experimental results can be scalable to the industrial scale, Garcia-Gonzalez et al. (2015) purposely kept the O2 concentration below the industrial safety margin (H2:CO2:O2=84:13.2:2.8) and obtained a biomass accumulation of 19 g/L and PHB content of 61% using a two-stage cultivation system. Given a gas mixture is used as the carbon source for cell growth, Lu and Yu (2017) proposed to use a packed-bed reactor instead of a stirred tank reactor to improve the mass transfer between cells and feed gas, resulting in a biomass accumulation of 5 g/L and PHB content of 67%. Other than mixing CO2 with H2 and CO2 as a carbon source, synthetic gas (syngas), which is a common industry effluent produced from pyrolysis and steam reforming, can be directly used as the carbon source for PHB production (Liu et al., 2014). Shin et al. (2021) utilized syngas (H2:CO2:CO:N2=20:20:20:40) to achieve a biomass accumulation of 33.8 g/L and PHB content of 42%. In recent years, many researchers started to adopt metabolic engineering techniques for more efficient PHB production from CO2. Tang et al. (2020) constructed a recombinant strain by gene modification in C. necator to achieve a cell accumulation of 0.55 g/L and PHB content of 50.4%. Similarly, Miyahara et al. (2020) inserted a gene encoding PHA synthase 1 from Pseudomonas sp. into C. necator to better utilize CO2. In addition, since H2 oxidation is required for cell growth, to avoid explosion during the fermentation process, Miyahara et al. (2020) utilized a gas mixture with a composition of H2:CO2:O2:N2= 3.6:12.3:7.6:76.5. With such a low H2 concentration, a biomass accumulation of 0.385 g/L and PHB contents of 70% were achieved. Likewise, Lambauer and Kratzer (2022) recently reported a lab-scale cultivation of C. necator on an explosive gas mixture of H2, CO2, and O2 in a ratio of 85:10:2. The results showed that the CO2 was fixed during the cultivation and that approximately 98% of the produced PHB was formed from CO2. Indeed, the gene for CO2 fixation has been identified in C. necator, which allows its heterotrophic growth using CO2 as a carbon source (Bellini et al., 2022).
- Fully compostable or infinitely reusable (bio)polymers
As opposed to the mechanical recycling process that shreds the polymers into progressively shorter chains, a company[4] spun out of the Lawrence Berkeley Lab devised a chemical recycling process using an acid that decomposes the polymers back into their original monomer structures. It also allows the monomers to be separated from entwined additives. This theoretically enables it to be infinitely recyclable, never losing its original performance characteristics. Moreover, while first made using petrochemical building blocks, advanced over the last four years detailed in a paper published this year have replaced those with microbially fermented corn stover. The researchers produced a PDK with ~80% bio-content and say there’s a feasible path to 100%.
Making the initial resin requires a massive upfront investment on both axes but the cost to recycle is commercial competitive with the most universal plastics in use today and its GHG emissions are lower. Thus, it’s true lifecycle metrics depend heavily on how many times it’d get recycled in practice.
This second graph shows the above metrics for the biorenewable version and models two possible scenarios with improved production yields. In the ‘intermediate’ scenario, yields reach ~50% of the theoretical maximum (0.35 g bioTAL per g of glucose, 0.315 g bioTAL per g of xylose) and an ‘optimized’ scenario represents a mature facility in which yields reaches ~90% of theoretical maximum (0.63 g bioTAL per g of glucose, 0.567 g bioTAL per g of xylose) and all process parameters have been optimized to reach a practical minimum production cost. These results suggest the feasibility of diverting polymers from the land fill in a way that’s competitive on both economic and environmental planes. Increasingly optimized processes over time may outcompete on multiple axes.
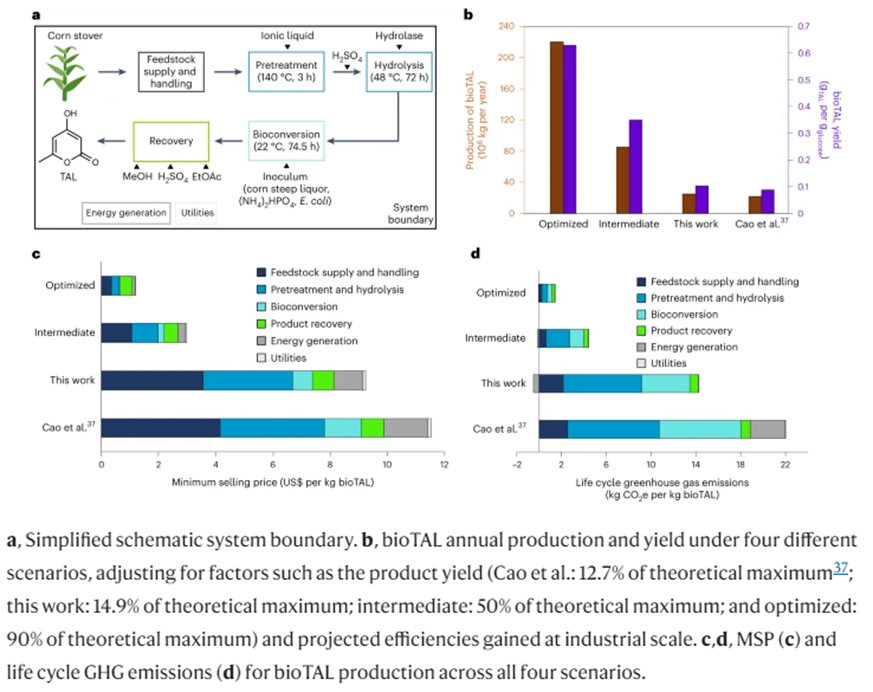
- Additives for otherwise non-degradable polymers to make them programmatically degrade
Another company spun out of Lawrence Berkeley created a process that embeds enzymes that break down polymers into the concoction of additives and polymers during the plastics’ creation. This ensures they are present in sufficient quantities, evenly dispersed throughout the material, and available for the job when called upon. In comparison to this process, recycling facilities currently pour the enzymes on top of the solid plastic at life cycle end, resulting in the enzymes being poorly distributed and unable to get into the molecular fabric of the material.
The group’s studies pushed the field’s understanding of the other rate limiting factors of enzyme-containing plastics. They found that additives fundamentally change the polymer’s molecular structure, causing the polymer chains ends to bend and twist and often become immobilized as if woven into the membrane. Enzymes, as represented by the Pac-Man like characters in the graphic below, must bind to the ends of loose chains in order to chomp away and break down the polymers into monomers.
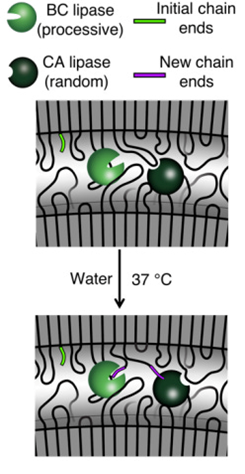
The group addressed the immobilization of chain ends by introducing an enzyme that cuts them in two, leaving chain ends for the other enzyme to bind to. The group’s final advancement was to surround the enzymes with a protective coating to ensure they remain alive and functional by the time they’re called upon to act. These tricks helped the group achieve near-complete degradation (>95% under mild conditions of 30 degree Celsius water).
Degradation was triggered only by heat, water, and time. A polyester shirt would withstand sweat and washing at moderate temperatures, for instance. Soaking the polymer fibers in water for three months at room temperature didn’t cause it to degree. With greater heat, however, it quickly degrades. In industrial composting circumstances of 50°C, the modified PLA degraded in six days and the PCL in two days at 40°C.
- Degradation of existing plastics
Plastic degrades naturally, just over very long time periods. What’s doing the degrading? Microbes. So a popular approach[5] to degradation of existing heaps of plastic has been to find microbes that already have a penchant for the job and then engineer them to do it faster. Allonnia, a spin out of Gingko, takes samples from waste sites, isolates which areas are showing the most activity, and applies synthetic biology tactics to boost the microbes’ performance. NC State took the polymer eating gene from one bacteria and put into one that reproduces exceptionally fast in salt water. Another company called Protein Evolution is collaborating with Department of Energy scientists to apply AI to improve the enzyme design by analyzing millions of unique mutations. Its enzymes currently feed on polyester waste to churn out PTA that’s indistinguishable from petroleum-derived monomers but with a far lower carbon footprint. A final example is from Wyss, which characteristically added a bit of flair to the enzymatic recycling process. They devised a system of two different microbial species working together to break down PET and subsequently generate the desired products of interest. The division of labor enables them to pick species that were optimal for its specific task. As nature works via systems-level organization, this seems like a fruitful area of research for further exploration.
To get a sense for where synthetic biology can take us, consider the abstracts of two recent studies applying the latest in AI to explore new PET-eating enzymes and to design an improved version based on desired parameters:
To date, reported PET hydrolases have been sourced from a relatively narrow sequence space. Here, we identify additional PET-active biocatalysts from natural diversity by using bioinformatics and machine learning to mine 74 putative thermotolerant PET hydrolases. We successfully express, purify, and assay 51 enzymes from seven distinct phylogenetic groups; observing PET hydrolysis activity on amorphous PET film from 37 enzymes in reactions spanning pH from 4.5–9.0 and temperatures from 30–70 °C. We conduct PET hydrolysis time-course reactions with the best-performing enzymes, where we observe differences in substrate selectivity as function of PET morphology. We employed X-ray crystallography and AlphaFold to examine the enzyme architectures of all 74 candidates, revealing protein folds and accessory domains not previously associated with PET deconstruction. Overall, this study expands the number and diversity of thermotolerant scaffolds for enzymatic PET deconstruction.
Application of PET hydrolases, however, has been hampered by their lack of robustness to pH and temperature ranges, slow reaction rates and inability to directly use untreated postconsumer plastics11. Here, we use a structure-based, machine learning algorithm to engineer a robust and active PET hydrolase. Our mutant and scaffold combination (FAST-PETase: functional, active, stable and tolerant PETase) contains five mutations compared to wild-type PETase (N233K/R224Q/S121E from prediction and D186H/R280A from scaffold) and shows superior PET-hydrolytic activity relative to both wild-type and engineered alternatives12 between 30 and 50 °C and a range of pH levels. We demonstrate that untreated, postconsumer-PET from 51 different thermoformed products can all be almost completely degraded by FAST-PETase in 1 week. FAST-PETase can also depolymerize untreated, amorphous portions of a commercial water bottle and an entire thermally pretreated water bottle at 50 ºC. Finally, we demonstrate a closed-loop PET recycling process by using FAST-PETase and resynthesizing PET from the recovered monomers. Collectively, our results demonstrate a viable route for enzymatic plastic recycling at the industrial scale.
Read next section: textiles, beauty products & home goods
[1] Sources saying it’s $9B1, $12B in 20181
[2] See here for the DoE’s Strategy for Plastics Innovation Report.
[3] Lignin is a major byproduct of industrial pulping processes (∼70 Mt per year); however, only ∼2% is currently used, while the rest is incinerated.34 Chemists have made enormous progress in depolymerizing lignin into discrete, highly functionalized chemicals (mainly phenolics).33 However, polymerization processes that utilize lignin still suffer from the aforementioned disadvantages and, at the same time, do not mitigate the existing plastic waste crisis. (link)
[4] The company has strong leadership: in addition to a lead inventor of PDK serving as an advisor, the CEO was previously the Global Business Director / General Manager at DuPont and another adviser was the co-founder of Amyris
[5] To dig deeper into the literature, see the papers cited in this work